1. Introduction
In general, importers or distributors are more focused on distribution channels, marketing, and commercial aspects. However, when they are searching for an ODM/OEM manufacturer, they always ensure they shop around before making a decision. Imagine this product involves some unknown techniques; unless you invent a product from scratch, it is difficult to determine the exact cost. In this article, let’s discuss how non-insiders can analyse the cost of every part of the PI-02!
2. Difficulties in Studying the Costs of Other Manufacturers
If you ever visit our neighbouring country and try to purchase pitchers, you may hear this kind of conversation from the factory owner or the sales person: “The quality is definitely no problem,” “We definitely use raw material, never recycled material,” “We promise we never cut corners,” “We export a lot of containers to India and Dubai every month.” Then, they always very warmly persuade you to accept their invitation to their banquet, in order to secure the business. After a few glasses of wine, you end up totally forgetting to ask about the cost of the pitchers.
3. Understand the Cost Structure of PI-02 Pitcher
Let us take PI-02 as an example for further exploration. In the same pitcher production, different manufacturing designs can necessitate varying components. Some designs might require 10 different parts while others might only need 7 parts. Naturally, the cost will be higher when more parts are required, and the assembly wages will increase. There is also a greater probability of an increased defect rate and various losses.
Now, regarding material selection, the usual choices are: AS Resin (Polystyrene), ABS (Acrylonitrile), PP (Polypropylene), or a Silicone water-stopping washer.
4. Filter material is also a focal point for pitcher cost
The price can vary due to the quality and quantity of filter material used. Generally, a standard filter is filled with 80% silver-impregnated granular activated carbon and 20% food-grade low sodium ion resin.
So why do we use silver-impregnated granular activated carbon? And why do we use low sodium ion resin?
We know that silver can kill bacteria. After activated carbon is treated with silver, it can also inhibit bacterial growth. Naturally, the cost is higher, much higher in fact.
When ionic resin exchanges with water, it releases sodium ions. If the human body absorbs too much water containing sodium ions, it can result in blocked blood vessels. Therefore, we need low sodium ion resin. Low sodium ion resin is a special filter material, hence its price is relatively higher than others.
On the other hand, the price will be significantly different if common activated carbon and common cationic resin are used.
Of course, sometimes customers will insist on using 100% common activated carbon. This needs to be considered when calculating the cost.
5. Must understand the weight of every part
The most convenient way is to ask the supplier to provide the weight of each part of the pitcher. If there is difficulty in obtaining this information, then take a sample, disassemble it, and weigh each part. Once you have the weight of each part, the cost of the component can be calculated.
6. The Material of Every Part
Next, we need to understand the materials used for the pitcher. The price of different plastic materials can vary significantly per kilogram. Manufacturers typically choose materials based on hydrophilicity, impact resistance, non-toxicity, and cost-effectiveness. Generally, it is composed of the following components:
Clear plastic shell: Used for holding filtered water. The material is usually AS Resin (Polystyrene).
Funnel: Supports the filter and holds unfiltered water. The material is ABS (Acrylonitrile).
Filter shell and filter cover: These hold the silver-impregnated granular activated carbon and low sodium ion resin water filter material. The material is also ABS (Acrylonitrile).
The lid and spout lid: Used to prevent dust from falling in. The material is ABS (Acrylonitrile).
Water stopping washer: Generally made from non-toxic silicone material, it is used to cover the periphery of the filter to prevent leakage.
7. Additional Function for the Pitcher
For the convenience of users, manufacturers usually add an extra function when designing the pitcher – a filter replacement reminder. To prevent moisture, they typically choose a mechanical reminder.
To make the product more advanced, they may opt for an electronic reminder. The cost is between USD$1-2 each.
8. Packaging
And then, is to give the product a beautiful boxing. A colorful cardboard box cost about USD$ 1 – 1.2 /EACH. In order to prevent little cockroach and insects, some of manufacturers will choose to use shrink film on the outside of the color box.
9. Cost Calculation
The author lists the current prices of plastics, filter materials and some detailed costs as below. You can calculate the cost of a pitcher by the above method, plus the packaging, manual, shrink film, etc.
1.Assembly salary: USD$0.37 – $0.56 /each
2.Outer Packaging: USD$0.19 – $0.30 /each
3.Shrink film packaging: USD$0.11 – $0.15 /each
4.Color box cost: USD$0.60 – $1 /each
5.Instruction manual: USD$0.04 – $0.07 /sheet
6.Non-woven fabric filter: USD$0.07 *2PCS = USD $0.14
7.Logo printing cost: USD$0.37 – $0.56 /each
8.Loss: 1%
9.Price of filter material in July.2021:
Silver impregnate granular activity carbon:USD$5.56/per kg
Low sodium ion resin:USD$14 – $15.50 /per kg
O-ring:USD$0.11 – $0.19/each
10.Price of plastic material in July.2021:
AS Resin【Polystyrene】:USD $2.60 /per kg
ABS【Acrylonitrile】:USD $2.89 / per kg
10. Injection Salary
This entails a comprehensive grasp of the mould developed by the manufacturer, the injection moulding time, the size of the injection moulding machine, etc., in order to accurately calculate the cost.
1.Mold Development Effects on Injection Cost
1.1 Modulus in the mold: The higher the modulus, the more expensive the mold cost. Therefore, faster production of finished products results in lower product costs.
1.2 If the mold is designed for automatic gripping by a mechanical arm, the mold cost will be higher. Conversely, eliminating the need for labour can reduce injection costs.
1.3 The mold design using slides and the incorporation of the brand logo directly onto the plastic shell eliminates the need for additional printing processes, saving on labour costs. However, the mold itself will be more expensive.
Injection Moulding Cooling Time
2.1 Utilising a cooling water system in the injection moulding machine can reduce the cooling time of the plastic material in the mould, thereby increasing output.
The Size of the Injection Moulding Machine Used
If the mold maker lacks expertise and designs the mold too large, a larger injection moulding machine will be necessary. This will result in higher electricity consumption and reduced flexibility compared to a smaller injection moulding machine. Therefore, all moulding designs, injection moulding machine sizes, and related details must be thoroughly checked with the factory before requesting a quotation.
11. Profit
Manufacturers require higher profits to sustain operations. Not only is it necessary to allocate some profit for new product development, but also for expanding product capacity, increasing automated machinery, equipment, and purchasing land to expand the factory. A gross profit margin of 20-30% for a factory is not excessive, considering the need to deduct management expenses. Additionally, the purchase volume affects the price, with the possibility of price reduction only feasible for batch quantities exceeding 10,000 or for projects with high competitiveness in the market.
Author: Rodger Lin, July 4, 2021
“Welcome reproduction, please indicate the resource.”
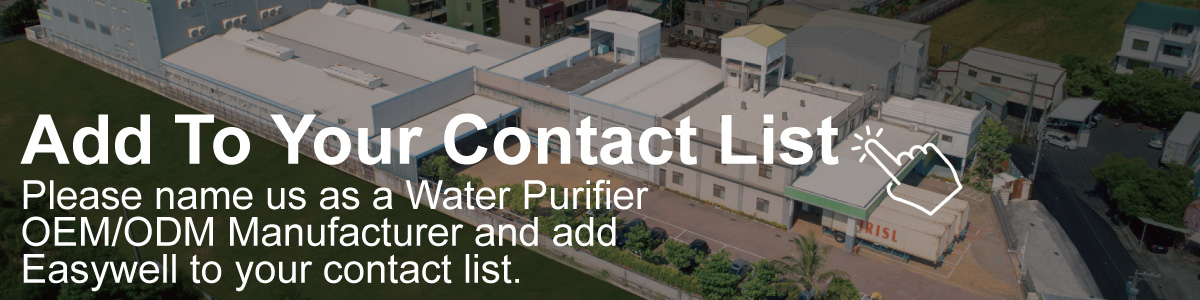